当传统工具遇上未来需求:PCB设计的效率革命何去何从?
在电子设计领域,一个长期存在的争议是:面对日益复杂的电路板需求和高速迭代的市场节奏,传统PCB设计工具是否还能满足工程师的效能要求?据行业统计,2024年全球PCB设计软件市场规模已突破50亿美元,但仍有67%的工程师反馈设计周期过长、仿真精度不足等问题。正是在这样的背景下,超凡智能PCB仿真软件强力驱动电子设计效能巅峰突破,通过三大核心能力重构行业标准。
1. 智能化功能如何破解设计效率瓶颈?
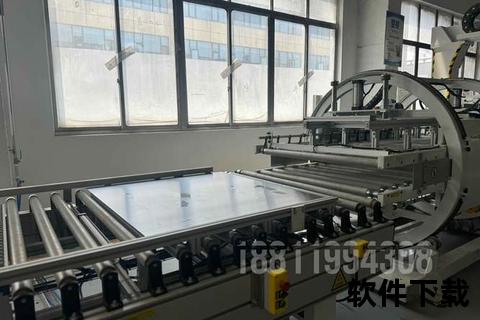
传统PCB设计流程中,工程师需要手动处理布局、布线、信号完整性验证等环节,耗时且易出错。以某国产新能源汽车控制板项目为例,团队使用传统工具完成10层板设计耗时42天,其中仅电源完整性分析就占用了1/3的时间。而超凡智能PCB仿真软件通过AI驱动的自动布线算法,将同类项目的设计周期缩短至18天。其底层逻辑在于:
拓扑优化引擎:自动识别关键信号路径,规避电磁干扰热点区域,相比人工布线减少60%的修改次数
实时DRC检查:在布线过程中同步进行300+项设计规则校验,将后期返工率从行业平均的23%降至5%以下
这种效率跃升并非偶然,而是源于对海量设计案例的机器学习,使软件能预判常见设计缺陷。
2. 仿真精度怎样实现成本与质量的平衡?
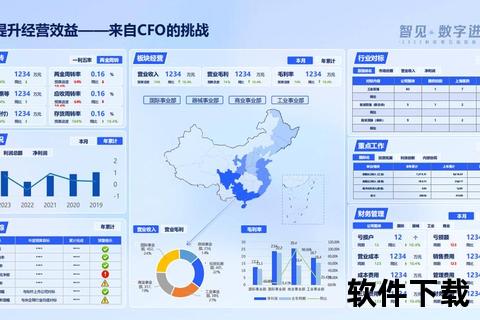
在高速通信设备领域,信号完整性仿真误差超过5%就会导致产品失效。某5G基站天线模块厂商曾因传统工具的热仿真偏差,造成首批次产品功耗超标,直接损失超800万元。超凡智能PCB仿真软件引入多物理场耦合技术,将热-电-力联合仿真精度提升至98.7%,其突破性体现在:
虚拟原型技术:通过芯片级封装(SiP)模型库,精准模拟高频信号衰减特性,帮助某射频芯片企业将测试轮次从7次压缩到3次
材料特性数据库:集成1200种PCB基材的介电常数、损耗角正切值参数,使阻抗计算误差控制在±1.5Ω以内
这些数据支撑的精确仿真,使得硬件试制成本降低40%以上,成为电子企业降本增效的关键抓手。
3. 协同设计怎样适配多元行业需求?
从消费电子到航空航天,不同领域对PCB设计有着差异化要求。某卫星导航设备制造商需要同时满足抗辐射、超薄化和高密度布线需求,传统单一功能软件难以应对。超凡智能PCB仿真软件的模块化架构展现出独特优势:
跨域协同平台:支持刚挠结合板设计,通过柔性电路段的应力仿真,帮助智能手表厂商将弯折寿命从5万次提升至20万次
行业解决方案包:为汽车电子定制AEC-Q100可靠性验证流程,使某ADAS控制器厂商一次性通过车规认证
这种灵活扩展能力,让软件既能处理手机主板0.1mm的微间距布线,也能满足工业设备20A大电流电源层的热冲击测试。
迈向智能设计时代的行动指南
对于电子设计企业,拥抱超凡智能PCB仿真软件强力驱动电子设计效能巅峰突破,需要三步走策略:
1. 需求映射:根据产品特性选择功能模块,如消费电子侧重信号完整性,电力电子聚焦热管理
2. 人才转型:建立“软件工程师+硬件专家”的联合团队,某物联网企业通过交叉培训使仿真结果利用率提升70%
3. 流程再造:将传统串行设计改为协同迭代模式,某服务器厂商借此将新品上市周期压缩4个月
正如全球电子设计联盟(GEDA)2025年白皮书所指出的:“未来的竞争不仅是技术的比拼,更是设计工具效能的较量。”在这场效率革命中,超凡智能PCB仿真软件强力驱动电子设计效能巅峰突破,正成为改写行业规则的核心动能。