激光打标行业的技术困局:高效与精准能否兼得?
在工业制造领域,激光打标技术凭借“永久标记”和“无接触加工”的优势,已成为医疗、汽车、电子等行业的标配工艺。随着市场对产品追溯性和个性化需求的提升,传统激光打标技术暴露出两大痛点:人工依赖度高导致效率瓶颈,以及复杂材料与精细图案难以兼顾精度。例如,某手机配件厂商曾因打标位置偏移导致批量产品报废,损失超百万元;另一家电梯面板制造商则因雕刻立体花纹时出现毛边,被迫延长30%的质检工时。
这些问题背后,是传统设备对人工定位、固定光斑模式和单一软件功能的过度依赖。如何突破这一困局?超凡高效激光打标软件智能升级精准雕刻新境界的解决方案,正通过三大技术革新重新定义行业标准。
一、智能视觉定位:如何让误差小于0.01毫米?
传统激光打标需要依赖精密治具定位,每更换一次产品型号就意味着数万元的治具投入和数周的调试周期。而搭载高精度CCD视觉系统的智能软件,通过“先拍照、后打标”的模式,实现了“无治具化”生产。以深圳某U盘制造商为例,其流水线上的U盘因来料位置随机偏移,传统打标良品率仅为78%。引入视觉定位系统后,软件通过实时捕捉产品轮廓并计算偏移角度,将打标精度控制在±0.01mm内,良品率跃升至99.5%。
更值得关注的是,这类系统支持多产品同时识别。浙江某五金企业采用视觉软件后,单次可完成12个螺丝帽的自动定位打标,效率提升4倍,人力成本降低60%。这标志着激光打标从“机械定位”向“AI视觉”的跨越,超凡高效激光打标软件智能升级精准雕刻新境界的核心竞争力初现。
二、动态光斑调节:怎样在镜面不锈钢上雕刻发丝级纹路?
在高端装饰材料领域,客户既要求雕刻深度均匀,又追求如发丝般细腻的线条表现。传统设备的固定光斑模式难以兼顾两者,而可变光斑技术的突破彻底改变了这一局面。以创可激光的超大幅面光纤打标机为例,其搭载的2.5英寸光学聚焦系统可将光斑直径缩小至传统设备的50%,线宽达0.2mm,同时通过散焦控制实现深度0.01-0.5mm的无级调节。
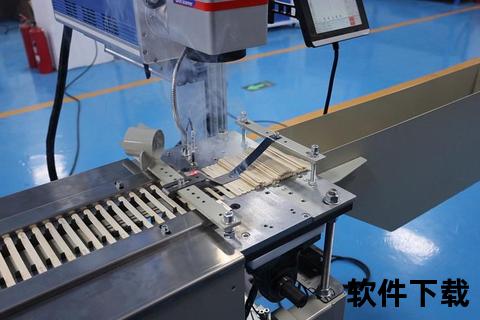
这一技术的商业价值在卫浴行业得到验证。某品牌龙头厂商需要在镜面不锈钢上雕刻0.3mm宽的品牌LOGO,传统工艺因热影响区过大导致边缘氧化变色。采用动态光斑技术后,软件根据预设参数自动切换光斑大小:粗光斑快速去除表层,细光斑精修轮廓,最终在保持镜面光泽的同时实现浮雕效果,订单交付周期缩短40%。超凡高效激光打标软件智能升级精准雕刻新境界,正是通过这种“粗细自如”的光学控制,打开了精密加工的新维度。
三、软件生态融合:为何说“一键造物”不是神话?
激光打标的效率瓶颈不仅在于硬件,更受限于软件生态的割裂。传统设备需要操作者在CorelDRAW设计图形、Photoshop处理位图、专用软件生成序列码,流程繁琐且易出错。新一代智能软件通过多格式兼容+自动化编码,真正实现了“设计-打标”无缝衔接。
典型案例来自东莞某模具厂。该企业每天需在数千个模具上标记包含日期、二维码和自检数据的复合信息。过去操作员需手动输入20余项参数,耗时长达3分钟/件。引入支持PLT/DXF/BMP格式直读、自动生成DataMatrix码的软件后,系统直接调用ERP数据批量生成标记方案,单件处理时间压缩至20秒,错误率归零。更有革命性的是LaserMaker等国产软件推出的“一键造物”功能,用户可从图库中选择齿轮、木盒等三维模型,软件自动生成切割路径和支撑结构,使非专业人员也能完成复杂结构制作。这标志着超凡高效激光打标软件智能升级精准雕刻新境界已从单一加工工具进化为智能制造枢纽。
破局者的行动指南
对于企业而言,拥抱激光打标智能化需分三步走:
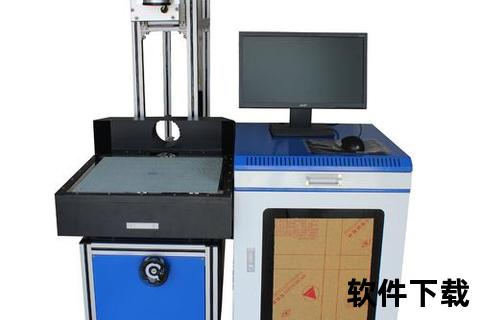
1. 优先选择集成视觉定位的系统,特别是在小件多品种场景中,可减少90%的治具投入;
2. 关注光斑动态调节能力,优先测试设备在0.1-1mm线宽范围的稳定性,确保复杂图案的精细度;
3. 评估软件生态兼容性,选择支持CorelDRAW/AutoCAD文件直读、自动编码跳号的平台,避免数据转换损耗。
据华经产业研究院预测,到2025年,搭载智能软件的激光打标设备市场规模将突破80亿元,其中动态光斑和视觉定位技术的渗透率将达67%。这场由软件驱动的技术革命,正在将“精准”与“高效”从对立面转化为协同创新的双引擎。超凡高效激光打标软件智能升级精准雕刻新境界,不仅是技术迭代的产物,更是制造业向智能化跃迁的里程碑。